12 Mar 2025
How is the REEPRODUCE project recovering neodymium magnets from relevant waste streams?
The extraction of magnets from different waste streams plays a key role in the establishment of a rare earth elements value chain in Europe based on secondary resources and requires significant R&D as well as industrialisation efforts. HDDs and electric motors represent attractive sources for the recovery of NdFeB magnets from EoL products. These are applications where disassembly is attractive from an economical point of view due to the magnet quantities and the advantageous product properties. Electric vehicle traction drives are of central importance, as they contain attractive quantities and quality grades of rare earth magnets. In parallel, the automotive industry is a major driver of demand for rare earth elements.
Today, a large proportion of electronic waste is processed by shredding, which means that the magnets are lost in the ferrous fraction. To change this situation, fundamental research is needed with the aim of developing a universally applicable process chain.
Due to the increasing demand of rare earth magnets, the uncertainty of supply, and the growing waste streams containing rare earth elements, rapid industrialisation of the developed process chains is necessary. The REEPRODUCE project is performing pioneering work by demonstrating a practical level of industrialisation using the realised pilots. To do so, the machinery will be transferred to several European recycling facilities to be validated under real conditions. This is an important step towards meeting the objectives of the European economic strategy, which have been defined in the Critical Raw Materials Act.
In the context of the REEPRODUCE project, the Institute for Factory Automationand Production Systems (FAPS) of the Friedrich-Alexander-Universität Erlangen-Nürnberg(FAU) has developed the concepts to recover neodymium magnets from relevant waste streams. This includes both dismantling of end-of-life (EoL)products containing rare earth magnets as well as sorting processes for shredded ferreous fractions with a rare earth content.
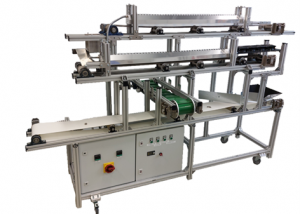
Pilots for efficiently extracting sintered neodymium-based permanent magnets from portable electric mobility devices’ wheels (above) and computer hard disk drive yokes (below), developed at FAU/FAPS.
Electric motors with different rotor configurations and hard disk drives are considered as part of the disassembly path. In the case of electric motors, three reference application shave been defined: electric vehicle drives, heating, ventilation and air conditioning (HVAC) compressors and traction wheels from personal mobility devices. For each application, a process chain has been developed, optimised and tested at bench-scale by FAU/FAPS. These processes have been upscaled at Bronneberg BV(BRO) and a common process line has been integrated into a mobile container with a corresponding automation system. Analogously, pilot process lines for the extraction of magnets from hard disk drives and shredded material have been realised.
By the end of 2024 the three pilots have been engineered and constructed based on previous research activities. The motor processing unit is currently under validation at BRO. In parallel, the HDD processing machine is currently tested at FAU/FAPS. The same applies to the sorting demo line for shredded ferreous fractions consisting of single test rigs which will remain at the institute for research purposes.
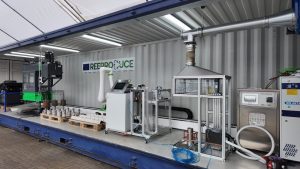
Pilots to extract Nd-based magnet blocks from components